Download summaries of this SMP and its maintenance guidance, with quick reference information for clients and developers:
Blue Roofs SMP One-Sheet
Blue Roofs Maintenance Guidance One-Sheet
4.6.1 Blue Roof Introduction
Blue roofs, also known as controlled flow roof drain systems, are detention stormwater management practices (SMPs) that provide temporary storage and slow release of rainwater on a rooftop. Blue roof systems are an effective practice for controlling runoff from buildings with flat or mildly sloped roof surfaces. On blue roofs, water is temporarily detained on the roof surface using rooftop check dams or roof drain restrictors. In all cases, outflow is controlled using orifices prior to discharge, which is typically directed to the building’s storm drains, scuppers, or downspouts.
Quick Tip
Required blue roof design and material standards are denoted in this Section by easy-to-reference numerals.
Since blue roofs function through detention and slow release alone, they neither add nor remove contaminants from stormwater; however, in a combined sewer area, they are acceptable pollutant-reducing practices for non-infiltrating Water Quality compliance. Blue roofs may also enable compliance with all remaining applicable Philadelphia Water Department (PWD) Stormwater Regulations (Stormwater Regulations), depending on outlet control sizing and structural and feasibility constraints. The designer is referred to Section 3.2.3 for information on using SMPs in series.
The design of blue roofs is not limited to the examples shown within this text. Successful stormwater management plans will combine appropriate materials and designs specific to each site.

When Can Blue Roofs Be Used?
In combined sewer areas where infiltration is not feasible, blue roofs can be used to meet Water Quality release rate and pollutant-reducing requirements.
A blue roof can be considered for installation on a fully built-out or highly-constrained site. They can be installed on many types of roofs, including terraces, high-rise building roofs, and low podium or at-grade on-structure installations.
Blue roofs can also be installed as a Stormwater Retrofit on existing buildings with flat, mildly sloped, or terraced roofs after confirmation of adequate structural loading capacity, waterproofing, and protection of rooftop utilities.
Key Advantages of Blue Roofs
- Manage stormwater runoff without occupying surface-level space
- Well-suited for sites at which roofs make up a large fraction of the total impervious area and for sites with ground-level space constraints
- Typically require no additional sewer connections besides the ones already provided for the building
- Easy to install if structural and waterproofing requirements are met
- Readily coupled with other SMPs, such as green roofs
- Can cost less than other SMPs
- Require no excavation
- Can provide educational benefits, especially when used at public and/or highly visible sites such as schools, recreation centers, libraries, etc.
- Assume less risk for projects within the floodplain
Key Limitations of Blue Roofs
- Require regular inspection and maintenance of roof surface and roof drains, especially following high winds, as algae and debris can develop around roof drains and limit the rate of discharge
- Require strict adherence to regularly scheduled inspections because the maintenance needs are not easily visible
- May have limited storage capacity with slopes greater than 2%, likely necessitating installation of roof check dams and/or terraces to meet release rate requirements
- May result in increased cost or limited Stormwater Retrofit opportunities for existing buildings and structures due to additional loading associated with ponded water on roof
- Offer limited benefit on sites where roof area makes up only a small fraction of the total impervious area
- Do not improve aesthetics or provide the ancillary environmental benefits associated with vegetated SMPs, such as habitat creation and improved air quality
Key Design Considerations for Blue Roofs
- Blue roof systems utilizing controlled flow roof drains generally require flat or nearly flat roofs (e.g., less than 2% slope). It may be feasible to use check dams when slopes are higher than 2%.
- All building mechanical systems, roof furniture, and other appurtenances installed on the roof should not be compromised by roof ponding during rain events and should not cause damage to the roof membrane.
- Blue roof drains should be located away from overhead trees, if possible, to prevent leaf litter that would result in the clogging of the drains and additional or prolonged ponding on the rooftop.
- In order to prevent damage to the waterproofing membrane, access to the roof should be limited to maintenance needs only. Pedestal pavers can be used to separate the blue roof from the walking surface.
- It is recommended that an easily accessible vantage point be created so as to facilitate visual inspection of the blue roof system after rain events. If the storage volume has not drained within the intended drain down time, a more thorough inspection of the roof surface and/or outlet controls should be performed.
- For any blue roof that discharges onto an adjacent property, a drainage easement may be required and is recommended.
Blue Roof Types
On roofs with a parapet, roof drain restrictor systems detain water on the roof, with eventual discharge to the existing roof drain.
Roof check dam systems detain rainwater on rooftops or sections of rooftops without a parapet to increase storage volumes over roof areas with greater than 2% slope. These dams create temporary ponding areas during rain events before slowly discharging to the roof drain.
4.6.2 Blue Roof Components
Figure 4.6‑1: Blue Roof with Typical Features
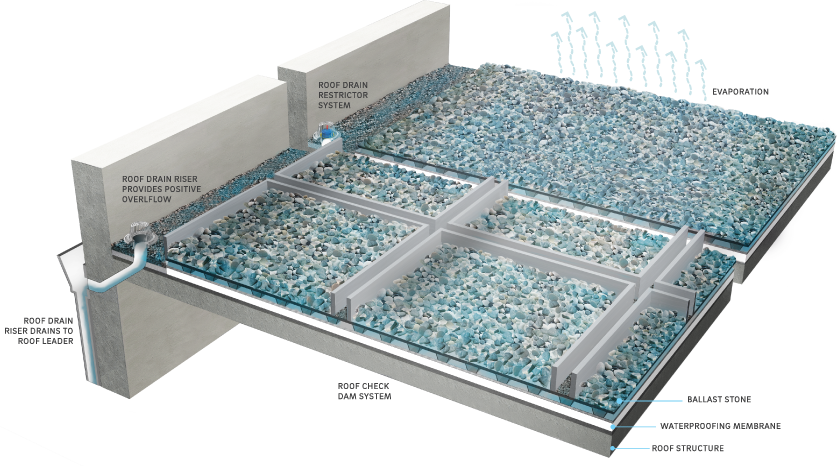
Inlet Control Component
Blue roofs that receive direct (1:1) rainfall only do not have inlet controls. For blue roofs that receive runoff from adjacent roof directly connected impervious area (DCIA), including additional roof levels, inlet control systems convey and control the flow of stormwater from the contributing catchment area to the SMP. The designer is referred to Section 4.11, Inlet Controls, for more information on inlet controls.
Storage Area Component
Blue roof storage areas temporarily hold stormwater until it can either evaporate or be released downstream at a controlled rate. The area dedicated to storage is dependent on the chosen blue roof system type.
Storage in roof drain restrictor systems is determined by the roof slope and geometry relative to the height of both the restrictors and parapets. The bulk volume occupied by all building mechanical systems, roof furniture, and appurtenances must also be factored into the storage volume calculations.
Storage in roof check dam systems is determined by the roof slope and associated area dedicated to ponding behind the dams. The bulk volume occupied by all building mechanical systems, roof furniture, and appurtenances must also be factored into the storage volume calculations
Blue roof storage areas are underlain by a waterproofing membrane. Numerous waterproofing membrane systems exist, including modified bitumen roofing (MBR), waterproof types of single-ply roofing, metal roof panels, spray polyurethane foam roofing, synthetic rubber membranes, thermoplastic membranes, and liquid-applied (including polyurethane-based and polymer-modified bituminous products) roofing. While high quality MBR systems (multiple MBR sheets tiled to reduce seam susceptibility) are suitable for blue roof usage, lower quality MBR systems (multiple layers of asphaltic sheets) are not recommended due to their seams that allow water to penetrate.
The durability and lack of seams achievable with a hot fluid applied, rubberized asphalt, fabric reinforced roofing system is well-suited for blue roofs. Cold liquid-applied systems are equally effective due to strict regulations on the use of the propane-fired devices for hot fluid systems.
Outlet Control Component
Outlet controls within a blue roof system can provide a range of functions, including the following:
- Meeting drain down time requirements;
- Controlling the rate of discharge from the SMP and limiting water surface elevations during various storm events; and/or
- Bypassing of flows from large storm events.
Outlet controls may include orifices, weirs, roof restrictors, risers, or impervious liners. The designer is referred to Section 4.12, Outlet Controls, for more information on outlet controls.
Roof drain restrictor blue roofs use a roof drain restrictor that is placed over the roof drain. These devices restrict flow through an orifice within the drain assembly, causing temporary ponding on the roof. They are typically purchased commercially through a manufacturer. Alternatively, a manufacturer can customize an orifice size for a specific development. The number and sizing of weirs and orifices are based on a predetermined relationship between the water depth approaching the drain and the flow rate entering the drain. The overflow mechanism of the device determines the maximum ponding depth.
For roof check dam systems, perforated aluminum T-section dams have been used to retain and slow release rainwater. These inverted T-sections are weather sealed and secured to the roof structure, creating ponding areas behind the dam. Perforations in the dam allow for slow release. If not commercially available, these dams can be easily fabricated.
Inspection and Maintenance Access Component
Safe and easy inspection and maintenance access to all major components within a blue roof system is critical to ensuring long-term performance. Dependent on roof height and slope, blue roof inspection and maintenance access components may consist of permanent or temporary safety monitoring systems, guardrail and safety net systems, warning line systems, and/or personal fall arrest systems. Inspection and maintenance access systems for blue roofs may also include long-term leak detection systems for locating and managing leaks.
4.6.3 Blue Roof Design Standards
General Design Standards
- Structural loading must be considered for all blue roof designs, and blue roof design must be coordinated with a licensed structural engineer for both new building construction and retrofits to existing structures.
- The maximum allowable surface ponding depth is four to six inches. This will depend on loading capacity of the roof; six inches represents roughly 32 pounds per square foot of dead load.
- The maximum allowable drain down time is 72 hours after the 24-hour storm event.
- Positive overflow must be provided for large storm events, up to and including the 100-year, 24-hour storm event, or, if the project is exempt from Flood Control, the ten-year, 24-hour storm. Overflow structures and pipes must be designed to convey at least the ten-year, 24-hour storm.
- Blue roof storage areas must be underlain by a waterproofing membrane.
Inlet Control Design Standards
- The designer is referred to Section 4.11, Inlet Controls, for information on design standards for inlet control systems.
Storage Area Design Standards
- The storage system must provide adequate storage to control release rates to meet all applicable Stormwater Regulations. The designer is referred to Section 3.2.3 for information on using SMPs in series.
- Designed storage capacity for blue roofs must account for structural and feasibility constraints. Connection to other SMPs can provide additional storage, if necessary.
- A porosity of 0.40 must be used for ballast stone.
- On roofs without ballast, designers must ensure that enough weight is provided to secure the waterproofing membrane. On roofs with ballast, designers must consider the depth and porosity of the ballast when calculating the potential storage volume.
Outlet Control Design Standards
- Roof drain restrictors must be sized according to the desired release rate and ponding depth.
- The designer is referred to Section 4.12, Outlet Controls, for information on design standards for outlet control systems.
Inspection and Maintenance Access Design Standards
- Safe access to blue roofs must be provided for periodic cleaning, inspection, and maintenance by trained building personnel. Easy access must be provided to each of the outlet controls, low-flow discharge points, and overflow connections to permit removal of debris under saturated conditions.
- Seams, corners, penetrations, mounts or platforms for mechanical utilities, and any other areas of the roofing membrane where risk of leakage is highest, must be inspected for damage or failure and repaired in a manner consistent with the membrane material.
4.6.4 Blue Roof Material Standards
Inlet Control Material Standards
- The designer is referred to Section 4.11, Inlet Controls, for information on material standards for inlet control systems.
Storage Area Material Standards
- Stone:
- Stone or gravel used for ballast within the stormwater storage area must be uniformly graded, clean-washed stone, either crushed or smooth. PWD defines “clean-washed” as having less than 0.5% wash loss, by mass, when tested per the Association of State Highway and Transportation Officials (AASHTO) T-11 wash loss test. AASHTO No. 3 and No. 57 stone can meet this specification.
- Stone size must exceed the mesh size of the outlet control screen or slots. Ballast stone typically falls within the size range of 3/8 inch to 2 inches.
- Ballast must meet all American Society of Testing and Materials (ASTM) D1863 requirements for mineral aggregate used on built-up roofs.
- Other materials may be allowable pending PWD approval.
- Waterproof Membrane:
- PVC, EPDM, and thermal polyolefin (TPO) are permitted.
- All waterproof membranes must meet appropriate ASTM specifications. PVC membranes must meet ASTM D4434 requirements, EPDM membranes must meet ASTM D4637 requirements, and TPO membranes must meet ASTM D6878 requirements.
- Waterproofing membrane must be fully waterproof with properly sealed seams, corners, and protrusions to prevent any intrusion of standing water above the membrane.
- Roofing membranes must meet all building code requirements and guidelines of the City of Philadelphia.
Outlet Control Material Standards
- The designer is referred to Section 4.12, Outlet Controls, for information on material standards for outlet control systems.
4.6.5 Blue Roof Construction Guidance
Proper construction of blue roofs is essential to ensure long-term functionality and reduce long-term maintenance needs. Blue roof systems are best installed by experienced roofing contractors with expertise in installing flat roof membranes over new or existing roof structures. A standard construction sequence for proper blue roof system installation is provided below. This can be modified to reflect different blue roof system applications or expected site conditions.
- Install waterproof membrane along the roof and parapet wall to a height at least six inches above the peak ponding elevation as per the SMP designs.
- Inspect for any irregularities that will interfere with drainage.
- Seal all edges, seams, corners, protrusions, and other anomalies in a watertight manner consistent with the installation specifications of the membrane manufacturer.
- Install outlet controls in a manner consistent with the City’s Building and Plumbing Codes and guidelines. The designer is referred to Section 4.12 for information on sizing and installation of outlet control systems. Outlet systems must include a bypass/overflow mechanism to permit rapid discharge when the storage volume of the blue roof system is exceeded.
4.6.6 Blue Roof Maintenance Guidance
Maintenance of blue roof systems focuses on the periodic removal of sediment and debris from outlet and storage areas in order to prevent clogging and limit deterioration of the roof membrane. Maintenance activities can generally be performed by individual building owners or site maintenance staff as needed. The contractor responsible for the installation of the rooftop system should be contacted immediately if it is not performing as designed.
Maintenance of roof assembly and waterproofing membrane will be dependent on the assembly type, age, and quality of roof components. As with any roof system, periodic inspections should be performed to assure that repair or replacement is not necessary.
Blue roof components are relatively easy to maintain due to their simplicity and ease of access. In the both roof check dam and roof drain restrictor systems, maintenance activities are readily conducted at the roof surface. All restrictors and ponded areas must be accessible for periodic inspection and cleaning.
Problems with a blue roof system generally fall into two categories: (1) the system drains too slowly, resulting in buildup of excess water on the roof for extended periods of time, bypasses of the controlled flow roof drains, or bypasses/overflows during small rainfall events; or (2) the system drains too quickly, due to leaking or other issues, exceeding the design drain down rate. If problems persist, a licensed professional should be consulted.
General recommended maintenance activities for blue roof systems are summarized in Table 4.6‑1.
Table 4.6‑1. Blue Roof Maintenance Guidelines
Early Maintenance Activity | Frequency |
---|---|
Inspect outlet structures, and storage areas for trash and sediment accumulation. | Monthly for the first year after installation to determine ongoing maintenance frequency |
Ongoing Maintenance Activity | Frequency |
---|---|
Remove debris from drainage outlets and outlet screens to prevent clogging. | During inspections or as needed to ensure performance |
Remove debris from secondary drainage/overflows. | During inspections or as needed to ensure performance |
Remove excessive buildup of sediment around the outlet controls or within the storage cells. | During inspections or as needed to ensure performance |
Inspect for leaks. | During inspections or as needed to ensure performance |
Break up ice formation around outlets and overflows. | As needed during winter months |
Maintain records of all inspections and maintenance activity. | Ongoing |
The designer is referred to Section 4.12, Outlet Controls, for information on maintenance guidance for outlet controls.