Download summaries of this SMP and its maintenance guidance, with quick reference information for clients and developers:
Green Roofs SMP One-Sheet
Green Roofs Maintenance Guidance One-Sheet
4.3.1 Green Roof Introduction
Green roofs, also referred to as vegetated roofs, eco roofs, and roof gardens, consist of a layer of vegetation that covers an otherwise conventional flat or moderately pitched roof. A green roof is composed of multiple layers which may include a waterproofing roof protection layer, moisture interception layer, drainage layer, leak detection layer, an engineered planting medium, and specialized plants. Through the appropriate selection of materials, green roofs can provide runoff volume reduction and runoff peak rate attenuation.
Quick Tip
Required green roof design and material standards are denoted in this Section by easy-to-reference numerals.
Green roofs can be combined with other stormwater management practices (SMPs) in series to meet the Philadelphia Water Department (PWD) Stormwater Regulations (Stormwater Regulations). The designer is referred to Section 3.2.3, for information on using SMPs in series.
The design of green roofs is not limited to the examples shown within this text, which focuses primarily on extensive green roofs. Successful stormwater management plans will combine appropriate materials and designs specific to each site.
Green roof design may be considered differently for Stormwater Retrofits. Designers looking to incorporate green roofs in Stormwater Retrofit projects should contact Stormwater Billing and Incentives for additional information.
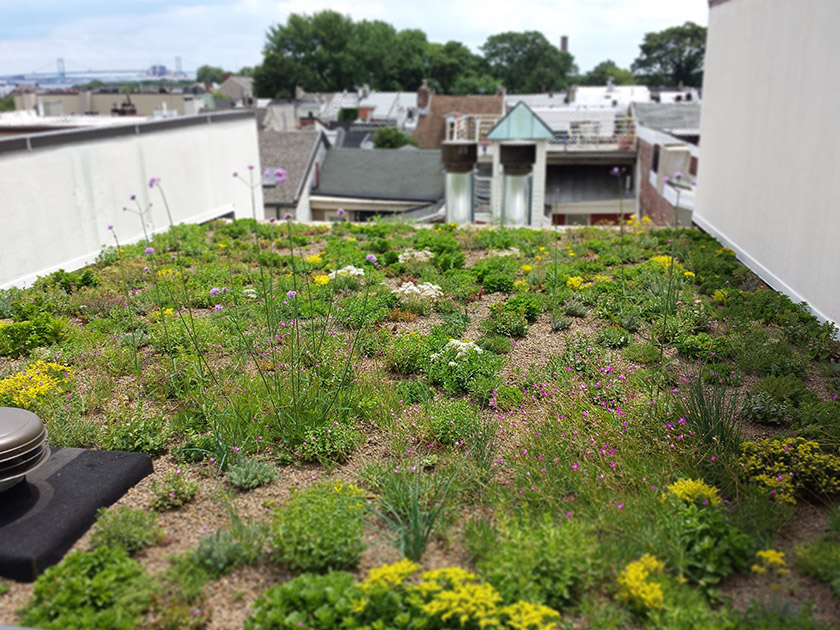
Where Can Green Roofs Be Used?
A green roof is an excellent stormwater management option on a fully built-out or highly-constrained site. They can be installed on many types of roofs, including terraces, high-rise building roofs, and low-podium or at-grade on-structure installations. Roofs with pitches up to 2:12 (16.7%) can, in most instances, accommodate green roofs without special slope stabilization provisions.
Green roofs can also be installed as a Stormwater Retrofit on existing buildings with flat, mildly sloped, or terraced roofs after confirmation of adequate structural loading capacity, waterproofing, and protection of rooftop utilities.
Tax Credit
Installation of a green roof may also qualify a project for a Business Income and Receipts Tax (BIRT) Credit!
Key Advantages of Green Roofs
- Manage stormwater runoff without occupying surface-level space
- Well-suited for sites at which roofs make up a large fraction of the total impervious area and for sites with ground-level space constraints
- Typically require no additional sewer connections besides those already provided for the building
- Promote the retention, slow release, and evapotranspiration of precipitation
- Enhance building aesthetics and market value
- Help regulate building temperature in both the summer and winter, thus reducing cooling and heating costs
- Reduce urban heat island effect by providing evaporative cooling
- Can improve air quality by filtering particulate matter
- Extend the service life of the roof by protecting the underlying roof membrane from mechanical damage, shielding it from UV radiation, and buffering temperature extremes
- Require no excavation
- Can be designed to provide spaces for recreation, supplement bird habitat, develop educational resources, and create new opportunities for urban food production
- Can provide a reduction in landscaping requirements for parking areas, as per Philadelphia Code § 14-803(5)(e.2)
- Can provide educational benefits, especially when used at public and/or highly visible sites such as schools, recreation centers, libraries, etc.
- Assume less risk for projects within the floodplain
- Eligible for inclusion in an Expedited Post‑Construction Stormwater Management Plan (PCSMP) Review project
Key Limitations of Green Roofs
- May need to be combined with other SMPs to meet the Flood Control requirement
- More expensive to install than most conventional roofs
- May have limited Stormwater Retrofit feasibility for existing buildings and structures due to structural capacity issues
Key Design Considerations for Green Roofs
- Coordination of green roof design with the design of building heating, ventilation, and air conditioning (HVAC) systems can help to maximize operational cost savings. For example, some research suggests that green roofs can improve building energy efficiency by lowering the temperature of air at the intakes for climate control systems.
- Stormwater management effectiveness can be improved by introducing measures to enhance evapotranspiration. Typical expedient measures include:
- Introducing low-transmissivity drainage layers;
- Lengthening seepage pathways to drains;
- Introducing rainfall interception layers;
- Selecting plants with dense root habits; and
- Selecting medium with high water-holding capacity.
- For extensive green roofs, at least half of the plants should be varieties of sedums. To ensure diversity and viability, at least four different species of sedum should be used. The remainder of the plants should be shrubs, herbs, meadow grasses, or meadow flowers, depending on the desired appearance.
- Green roofs should include a significant percentage of evergreen plants to minimize erosion in winter months.
- For stormwater management purposes, artificial, or synthetic, turf roofs are not considered green roofs and must be combined with other SMPs.
- For any green roof that discharges onto an adjacent property, a drainage easement may be required and is recommended.
Green Roof Types
There are two types of green roofs. An extensive green roof is a thin (usually less than six inches), lightweight system that is typically predominantly planted with succulents, drought-tolerant ground covering plants, and grass. An intensive green roof is a deeper (typically greater than six inches), heavier system designed to sustain complex landscapes. For intensive green roof profiles, a drain restrictor may be used to retain water in the base of the profile for subsequent plant transpiration.
4.3.2 Green Roof Components
Figure 4.3‑1: Green Roof with Typical Features
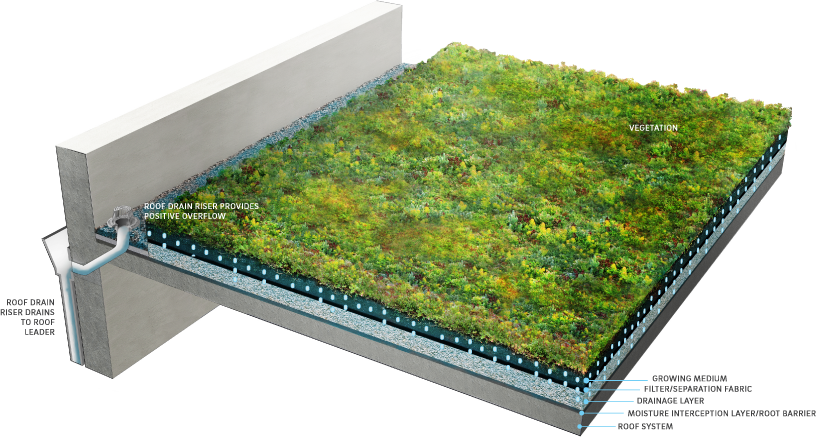
Inlet Control Component
Green roofs that receive direct (1:1) rainfall only do not have inlet controls. For green roofs that receive runoff from roof directly connected impervious area (DCIA), inlet control systems may convey and control the flow of stormwater from the contributing catchment area to the green roof. Distribution piping may be used to evenly disperse run-on water throughout the green roof. The designer is referred to Section 4.11, Inlet Controls, for more information on inlet controls.
Storage Area Component
Green roof storage areas temporarily hold stormwater before it can either be used by plants through evapotranspiration or be released downstream. Storage areas for green roofs typically are composed of the following components:
The growing medium supports plant growth and provides for storage of stormwater within voids. The storage capacity is a function of medium depth, surface area, and total void space. The growing medium may include foundation growth media (lightweight drainage aggregate) as a base.
Filter or separation fabric, or geotextile, prevents migration of soil into the underlying drainage layer of the green roof.
A drainage layer may incorporate measures to intercept and retain percolated rainfall as it moves through the green roof storage area. Examples include membranes with depressions to hold water and specialized fabrics or mats with high capillary indices.
Moisture interception layers/root barriers are impermeable liners that protect the underlying roof deck from moisture and plant root intrusion. Some waterproofing materials are inherently root resistant, whereas others require an additional root barrier.
Underlying roofing systems typically consist of a structural deck, its supporting structures, and a traditional overlying waterproofing system.
Vegetation Component
Green roof plant material is designed to take up much of the water that falls on the roof during a storm event. It mitigates wind and water erosion, transpires captured moisture back into the atmosphere, and provides evaporative cooling. Plant material also collects dust and creates oxygen. Some green roofs may also have irrigation systems to support plant growth during dry periods.
Outlet Control Component
Outlet controls may include risers, edge drains, scuppers, gutters, or impervious liners. The designer is referred to Section 4.12, Outlet Controls, for more information on outlet controls.
Inspection and Maintenance Access Component
Safe and easy inspection and maintenance access to all major components within a green roof is critical to ensuring long-term performance. Dependent on roof height and slope, green roof inspection and maintenance access components may consist of permanent or temporary safety monitoring systems, guardrail and safety net systems, warning line systems, and/or personal fall arrest systems. Inspection and maintenance access systems for green roofs may also include long-term leak detection systems for locating and managing leaks.
4.3.3 Green Roof Design Standards
General Design Standards
- Runoff from impervious roof area onto a green roof must be dispersed evenly across the green roof surface and pass through the growing medium either by sheet flow or a level spreading device. The designer is referred to Section 4.12, Outlet Controls, for design standards for level spreaders.
- The flow path of runoff across the green roof surface must be greater than or equal to the contributing DCIA length.
- Structural Requirements:
- Structural loading must be considered for all green roof designs, and green roof design must be coordinated with a licensed structural engineer for both new building construction and retrofits to existing structures.
- A structural engineer must verify that the building will support the weight of the green roof.
- Design calculations must consider the wet weight of the green roof. Extensive green roofs typically weigh between 20 and 45 pounds per square foot and are typically compatible with many wood or steel decks, as well as reinforced concrete or concrete fill roof systems. Intensive green roofs typically weigh more than 45 pounds per square foot and typically require reinforced concrete supporting decks.
- Potential maximum loads must be based on American Society of Testing and Materials (ASTM) E2397.
- The green roof area can be considered pervious open space when determining post-development flow rates to meet the Flood Control requirement. Default values for runoff parameters for extensive green roofs must be as follows; however, alternative runoff parameters may be applied when supported by submitted analysis and relevant references, which will be reviewed on a case-by-case basis:
- Natural Resources Conservation Service (NRCS) runoff curve number (CN): 86
- Composite runoff coefficient (CR): 0.40
- Time of concentration (TC): Six minutes
- The total amount of impervious surfaces within the designated boundary of a green roof footprint must not exceed one-third of the combined area.
- The following are exempt from being counted as tributary impervious area when installed on a green roof:
- Pervious pavers containing planted openings; and
- Drain chambers.
Inlet Control Design Standards
- If runoff is conveyed via piping, a distribution piping manifold must be embedded in a gravel strip to dissipate energy and promote uniform flow. The designer is referred to Section 3.4.2, for information on design standards for distribution piping.
- The designer is referred to Section 4.11, Inlet Controls, for information on design standards for inlet control systems.
Storage Area Design Standards
- For green roofs that receive direct (1:1) rainfall only:
- The minimum allowable thickness of the green roof growing medium is three inches. This can include both an upper finer-grained medium and a basal foundation growth media (lightweight drainage aggregate). The minimum allowable thickness of the foundation growth media is one inch.
- Green roofs that meet minimum growing medium thickness requirements are permitted a DCIA reduction equal to the entire area of the green roof.
- For green roofs that receive runoff from contributing impervious roof catchments:
- Impervious roof areas that direct runoff onto the green roof cannot exceed 50% of the green roof area, which is equivalent to a maximum hydraulic impervious runoff loading ratio of 0.5:1.
- The minimum thickness of the green roof growing medium must be calculated as follows, where the “impervious roof area to green roof area” ratio is less than or equal to 0.50:
Minimum thickness (in inches) of green roof growing medium = 3 inches + [3 * (Impervious roof area / Green roof area)] - Green roofs that meet minimum growing medium thickness requirements are permitted a DCIA reduction equal to the entire area of the green roof. Impervious roof areas that drain to these green roofs can be also considered as disconnected impervious cover, and, thus, included in the green roof’s DCIA reduction.
- In areas that will receive tributary discharge, the green roof must not include a high-transmissivity drainage layer, defined as a layer with a transmissivity of 0.005 m2/s or greater (ASTM D4716). In general, this will exclude peg-style or egg-carton-style geosynthetic sheets. High-transmissivity drainage layers will allow runoff to effectively flow under the green roof, minimizing contact with medium and plant roots. Typical granular aggregate, or coarse granular green roof medium, with a grain-size distribution complying with ASTM gradation No. 7 will satisfy the requirement, as will also a variety of mats and composite drainage layer assemblies.
- Any deck built atop a green roof that does not allow for sheet flow runoff must be slotted, and the minimum thickness of growing medium required for the green roof must be maintained under the entire extent of the deck.
- Saturated permeability of the growing medium, in its compacted state [ASTM E2399], must not be less than six inches per hour.
- Filter or separation fabric must allow root penetration, but prevent the growing medium from passing through into the drainage layer.
- A drainage layer is required to promote aerated conditions in the growing medium and to convey excess runoff during large rainfall events. The drainage layer must prevent ponding of runoff in the growing medium during the ten-minute maximum rainfall rate associated with the one-year storm.
Vegetation Design Standards
- When fully established, the selected plantings must thoroughly cover the growing medium.
Outlet Control Design Standards
- The contributing area of rooftop to each disconnected discharge point must be equal to or less than 500 square feet.
- Internal drainage, including provisions to cover and protect drains or scuppers, must anticipate the need to manage large rainfall events without inundating the cover.
- All drains and scuppers must be covered and protected by an enclosure, typically a square or round chamber with a locking lid. These chambers are designed to prevent clogging of the drains by debris.
- Although green roofs are not considered DCIA, they are not zero discharge systems. The roof drainage system and the remainder of the site drainage system must safely convey roof runoff to the storm sewer, combined sewer, or receiving water.
- The designer is referred to Section 4.12, Outlet Controls, for additional information on design standards for outlet control systems.
Inspection and Maintenance Access Design Standards
- Green roofs must be designed to allow for safe access and working conditions for green roof inspection and maintenance personnel. This access must be a permanent feature of the building, such as a pilot house, roof hatch, or exterior stairs to the green roof. Retractable, unsecured ladders should not be required for routine maintenance and inspections. The design may include other permanent personal safety measures. For green roofs, designers must specifically assess applicability to Occupational Safety and Health Administration (OSHA) Fall Protection Safety Standards and the American National Standards Institute (ANSI) and American Society of Safety Engineers (ASSE) consensus-based fall protection standards.
4.3.4 Green Roof Material Standards
Inlet Control Material Standards
- The designer is referred to Section 4.11, Inlet Controls, for information on material standards for inlet control systems.
Storage Area Material Standards
- Green roof growing medium must be a lightweight mineral material with a minimum of organic material and meet the following specifications:
- Moisture content at maximum water holding capacity (ASTM E2399 or FLL): 40% to 60% (vol)
- Porosity at maximum water holding capacity (ASTM E2399 or FLL): 10% to 15%
- Density at maximum water holding capacity (ASTM E2399 or FLL): ≤ 85 lb/ft3
- Total organic matter (MSA): 6% to 10% (dry weight)
- pH (MSA): 6.5 to 7.8
- Soluble salts (DPTA saturated media extraction): ≤ 2 mmhos/cm
- Water permeability (ASTM E2399 or FLL): 0.25 in/min to 1.25 in/min
- Grain-size distribution consisting of ≤ 4.5% passing for clay (0.002 mm) and 5% to 15% passing for silt (0.05 mm)
- The nutrients must be initially incorporated in the formulation of a suitable mix for the support of the specified plant materials.
- The medium must withstand freeze/thaw cycles.
- Foundation growth media (lightweight drainage aggregate) must be composed of blended media that meets the following specifications:
- Density at maximum water capacity (ASTM E2399-05): ≤ 65 lbs/ft3
- Maximum water holding capacity: 15% to 25%
- Water permeability (ASTM E2396-05): ≥ 25 in/min
- Total organic matter by loss on ignition (ASTM F1647): ≤ 1%
- Porosity (ASTM C29): 20% to 65%
- Grain-size distribution (ASTM C136) consisting of the following gradations:
- Pct. Passing US#18 sieve (1.0 mm): ≤ 5%
- Pct. Passing ¼-inch sieve: ≤ 30%
- Pct. Passing 3/8-inch sieve (9.5 mm): ≥ 75%
- Pct. Passing ½-inch sieve (12 mm): 100%
- Geotextile must consist of polypropylene fibers and meet the following specifications (American Association of State Highway and Transportation Officials Class 1 or Class 2 geotextile is recommended):
- Grab Tensile Strength (ASTM-D4632): ≤ 120 lbs
- Mullen Burst Strength (ASTM-D3786): ≥ 225 psi
- Flow Rate (ASTM-D4491): ≥ 95 gal/min/ft2
- UV Resistance after 500 hrs (ASTM-D4355): ≥ 70%
- Heat-set or heat-calendared fabrics are not permitted.
- Drainage Layer
- For vegetated roof cover assemblies with thicknesses of less than five inches, synthetic drainage layers may be used in lieu of granular drainage layers.
- For vegetated cover assemblies with an overall thickness of five inches, or greater, the drainage layer must meet the following specifications:
- Abrasion resistance (ASTM-C131-96): ≤ 25% loss
- Soundness (ASTM-C88): ≤ 5% loss
- Porosity (ASTM-C29): ≥ 25%
- Percent of particles passing 1/2-inch sieve (ASTM-C136): ≥ 75%
- The minimum thickness of the granular layer must be two inches. The granular layer may be installed in conjunction with a synthetic reservoir sheet.
- Waterproof Membrane/Root Barrier
- PVC, EPDM, and thermal polyolefin (TPO) are permitted and inherently root resistant.
- All waterproof membranes must meet appropriate ASTM specifications. PVC membranes must meet ASTM D4434 requirements, EPDM membranes must meet ASTM D4637 requirements, and TPO membranes must meet ASTM D6878 requirements.
- Waterproofing membrane must be fully waterproof with properly sealed seams, corners, and protrusions to prevent any intrusion of standing water above the membrane.
- Roofing membranes must meet all building code requirements and guidelines of the City of Philadelphia.
Vegetation Material Standards
- Use of invasive plants is not permitted. All plants must be appropriate and compatible with soil, hydrologic, light, and other site conditions. The designer is referred to Appendix I for plant lists.
- Perennials, grass-like plants, and groundcover plants must be healthy, well-rooted specimens.
- Green roof plantings must be able to withstand heat, cold, and high winds. After establishment, the plants must be self-sustaining and tolerant of drought conditions, with little to no need for fertilizers or pesticides.
- The only sedum known to be invasive and which must be avoided is sedum sarmentosum, also known as star sedum, gold moss, stringy stonecrop, or graveyard moss.
Outlet Control Material Standards
- The designer is referred to Section 4.12, Outlet Controls, for information on material standards for outlet control systems.
Inspection and Maintenance Access Material Standards
- Personal protection systems must comply with OSHA Fall Protection Safety Standards and the ANSI and ASSE consensus-based fall protection standards.
4.3.5 Green Roof Construction Guidance
- Apply waterproof membrane, and inspect for any irregularities that will interfere with drainage.
- Install root barrier layer, if required, and/or waterproofing protection layer.
- Install drainage layer.
- Install irrigation system, if included in design.
- Test the irrigation system, if included in design.
- Install filter or separation fabric layer over entire drainage layer.
- Install green roof growing medium, as specified.
- Establish vegetation.
- Green roofs can be effectively established by broadcasting fresh sedum cuttings during the spring and fall months. Depending on seasonal conditions, irrigation may be required after planting.
- Many perennial plants can be installed as plugs or container plants between April and November. Depending on the time of planting, temporary irrigation may be required.
- Perennials can be established from seed, except during the months of June, July, and August.
- A wind scour blanket or hydromulch may be required to prevent erosion during the establishment period. It generally takes about two growing seasons for full establishment. High wind environments may necessitate permanent wind blankets.
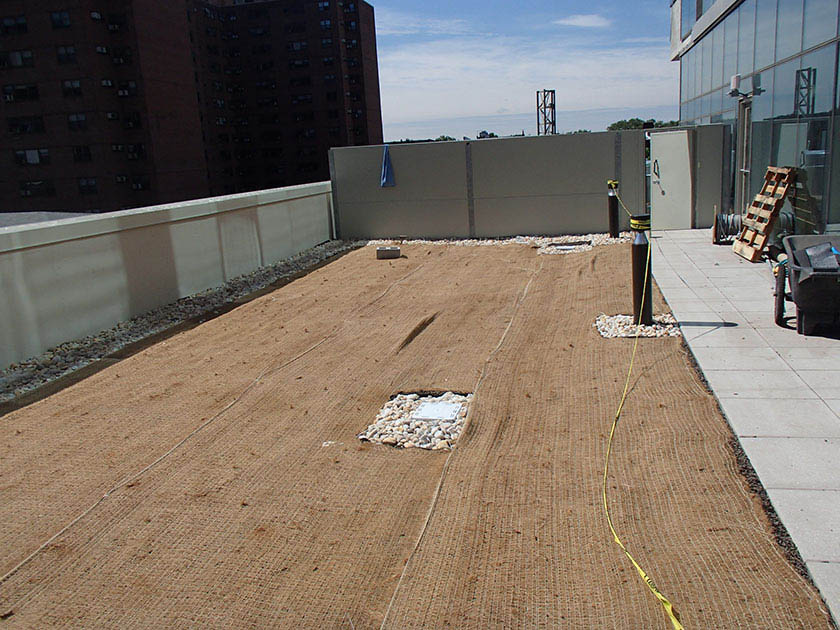
4.3.6 Green Roof Maintenance Guidance
Green roof maintenance activities largely focus on maintaining drainage capacity and the health of vegetation. All facility components, including plant material, growing medium, filter fabric, drainage layer, and waterproof membrane must be inspected regularly for proper operations, integrity of the waterproofing, and structural stability throughout the life of the green roof.
General recommended maintenance activities for green roofs are summarized in Table 4.3‑1 below.
Table 4.3‑1: Green Roof Maintenance Schedule
Early Maintenance Activity | Frequency |
---|---|
Water vegetation at the end of each day for two weeks after planting is completed. | Daily for two weeks after installation |
Water vegetation regularly to ensure successful establishment. | Every four days during periods of four or more days without rain, June through August for the first year after installation |
Hand-weed non-target/invasive plants | Four times per year for the first 24 months after planting |
Inspect vegetation for signs of disease or distress. | Biweekly for the first year after installation |
Ongoing Maintenance Activity | Frequency |
---|---|
Roof drains must be cleared when soil substrate, vegetation, debris or other materials clog the drain inlet. Under normal operating conditions, all roof discharge must be filtered and medium must not be vulnerable to migration toward the drains. Sources of sediment and debris must be identified and corrected. | As needed |
Plant material must be maintained to provide a minimum of 90% foliage cover during warm months. If coverage rate is declining, determine the reason (e.g., soil nutrition or soil moisture conditions) and implement remedial measures. | As needed |
Preferentially, weeding must be done manually, with herbicide use limited to extreme instances of weed infestations that compromise the plant cover integrity. Weeds must be removed entirely. | As needed |
Inspect root development. If root zone is not well developed, determine the reason (e.g., soil nutrition or soil moisture conditions) and implement remedial measures. | Quarterly |
Projects with permanent irrigation must be inspected and irrigation dosing rates adjusted to optimize plant performance and water use efficiency. | Quarterly |
Growing medium must be inspected for evidence of erosion from wind or water. If erosion channels are evident, a problem with the drainage system or with the green roof medium is indicated. Surface ponding or runoff must not occur except during very large rainfall events. After correcting the problem, refresh the affected areas with additional growth medium and provide temporary soil stabilization. | Quarterly |
Manually cut detrital herbaceous vegetation from the previous growing season to four to six inches above the ground. | Annually |
Inspect drain inlet pipe and containment system. | Annually |
Test growing medium for soluble nitrogen content. Fertilize as needed. | Annually |
During the plant establishment period, maintenance staff must conduct three to four visits per year to conduct basic weeding, fertilization, and in-fill planting. Thereafter, only two annual visits for inspection and light weeding is required (irrigated assemblies will require more intensive maintenance).
Use of herbicides must be avoided to prevent root penetration of waterproofing.
Fertilization must be applied according to soil test to maintain soluble nitrogen (nitrate and ammonium ion) levels between one and four ppm. The best source of nutrients for fertilization is mature compost.
Spill prevention measures from mechanical systems located on roofs must be exercised when handling substances that can contaminate stormwater.
The designer is referred to Section 4.12, Outlet Controls, and Section 4.13, Landscaping, for information on maintenance guidance for outlet controls and landscaping.